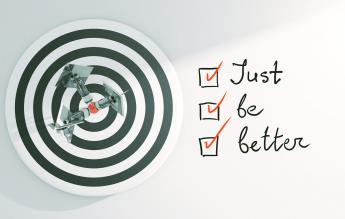
Les essais HALT et HASS ont pour objectif de construire la robustesse d'un produit principalement pendant le début de son cycle de vie.
Ils permettent de diminuer fortement, voire d'éliminer, les défauts de jeunesse d'un nouveau produit.
Les essais HALT, acronyme anglais de Highly Accelerated Life Test, reposent sur une succession de tests thermiques et mécaniques réalisée sur un équipement durant sa phase de conception.
La méthodologie appliquée permet de détecter des défauts et faiblesses de conception dans les équipements électroniques et leurs sous-ensembles. Non corrigés, ces défauts peuvent apparaître en cours de qualification en environnements (quand cette étape existe) ou une fois le produit commercialisé.
Les essais HASS, acronyme anglais de Highly Accelerated Stress Screen, sont des essais de déverminages. En production, tout ou partie de vos équipements sont soumis à des contraintes thermiques et mécaniques avec des niveaux de sévérités découlant des essais HALT. La méthodologie des essais HASS met en évidence des défauts liés au process de fabrication.
Ramenés au cycle de vie d'une série de vos produits, les essais HALT & HASS vous permettent d'influer sur les 3 phases décrites par le modèle de la courbe en baignoire représentant les variations du taux de défaillance en fonction du temps de fonctionnement.
Les essais HALT s'inscrivent dans la démarche des essais aggravés dont la philosophie est d'explorer le fonctionnement du produit en test au-delà de ses spécifications.
Concrètement, les stress thermiques et mécaniques seront appliqués sans tenir compte du profil de vie du produit. A priori, aucune limite de niveau de stress n'est fixée préalablement et des essais en vibration seront même appliqués pour un équipement fixe.
Les essais HALT n'ont pas pour objectif de simuler un environnement pour vérifier le bon fonctionnement d'un équipement, mais celui de stimuler un produit jusqu'à connaître ces limites de fonctionnement voir celles de destructions.
L'analyse des causes de défaillances et les actions correctives permettent de construire la robustesse d'un produit et éventuellement de dépasser les contraintes de son profil de vie pour encore augmenter sa fiabilité.
Les essais HALT s'adressent directement aux 3 sources de défaillances opérationnelles :
Défaut de fabrication
Défaut composants
Erreurs de conception
La méthodologie du HALT pour l’application de différents stress est la suivante :
Des contraintes spécifiques à l'équipement peuvent également être ajoutées.
Premier type d’essais réalisé, l’essai de tenue en température et plus particulièrement l’essai de tenue au froid.
Logique du procédé HALT, l’essai habituellement le moins destructif est réalisé en premier.
La caractérisation de la limite basse de fonctionnement en température, suivie de la limite basse de robustesse (voir de destruction, si celle-ci a lieu avant que la température "plancher" définie lors de la réunion préliminaire ne soit atteinte) se fait par un abaissement de la température par palier (ou STEP TEST).
Il est à noter que ces paliers doivent avoir une durée suffisante (généralement 10 min) pour que le déroulement correct des tests fonctionnels soit assuré mais aussi pour que la contrainte s’applique à un niveau stabilisé, en l’occurrence pour ce premier type d’essai lorsque les différents thermocouples disposés sur le produit attestent que la température de ses différents constituants est stabilisée.
Procédé dynamique permettant de construire la fiabilité d’un produit, le HALT ne se limite pas à une détection des seuils de fonctionnement et de destructions caractérisés via l’application de types de contraintes différentes.
Que ce soit pour l’essai de tenue en température ou pour les contraintes d’autre nature qui lui succède, le HALT permet de repousser les limites du produit par une approche dichotomique d’amélioration de la conception.
Pour chaque défaillance relevée est associée une analyse des causes premières de défaillances suivie d’actions correctives, et ce, en théorie, jusqu’à ce que la limite fondamentale de la technologie incriminée soit atteinte.
En outre, si une partie du produit ou un de ses sous-ensembles est identifié comme un maillon faible pour mener à bien une caractérisation complète du produit, le procédé HALT autorise (encourage ?) que le sous-ensemble soit isolé thermiquement (si c’est ce type de contrainte qui est en cours) ou même placé à l’extérieur de la chambre réalisant les tests pour peu que cette option soit techniquement fiable pour que la caractérisation complète soit menée à bien.
Conséquence de cette approche dynamique de construction de la fiabilité, l’essai de tenue aux Variations Rapides de Température (VRT) qui succède aux essais de tenue au Froid et au Chaud ne fait apparaître en moyenne qu’un pourcentage très faible de défaillances en comparaison aux autres types de contraintes (4% contre 14% pour la tenue au froid et 17% pour la tenue au chaud).
Connues par les fiabilistes comme un bon révélateur de faiblesse de conception, les VRT sont pourtant réalisées au maximum des capacités de la chambre, c’est-à-dire près de 70°C/min pour une enceinte HALT & HASS et avec une excursion en température définie par les limites hautes et basses de fonctionnement du produit identifiées dans les essais précédents.
En fait, ce paradoxe des taux de défaillance s’explique par lui-même dans le cadre de la méthodologie HALT : les essais de tenues au froid, puis au chaud ont fait apparaître des faiblesses de conception qui ont fait l’objet d’actions correctives et le produit testé en VRT est moins vulnérable aux contraintes thermiques que ne l’était celui qui a subi l’essai de tenue au froid.
A la tenue aux VRT, succède l’essai de tenue au vibration qui avec un taux de mise en évidence de défaillance de 45% devance le dernier type de contrainte appliqué dans le HALT, l’essai combiné vibration, température et VRT avec ses 20%.
La préséance des essais de tenue aux vibrations par rapport aux environnements combinés s’inscrit bien évidemment dans la même logique du HALT qui est de construire pas à pas la robustesse du produit.
L’essai de tenue aux vibrations suit une démarche analogue à l’essai de tenue en température avec un accroissement pas à pas du niveau de contraintes en accélération et avec le respect d’un temps de palier analogue.
L’uniformité de l’accélération dans le produit est réalisée après l’adaptation du montage solidarisant le produit testé avec la table de vibration ce qui est rendu possible par les mesures des différents accéléromètres disposés sur le produit qui fournissent la réponse du produit aux vibrations
A noter que du fait des différences , au niveau du produit testé, de la taille des composants et sous-ensembles et des différences de technologies mises en œuvre, la précipitation de défauts latents ne sera optimale qu’avec des excitations larges bandes aléatoires (les bandes basses 2 Hz - 1 kHz sont souvent causes de la défaillance de la plupart des composants électroniques et mécaniques grandes tailles et les bandes hautes, supérieures à 2 kHz, pour les éléments à haute fréquence de résonance comme les CMS.
Une exploration sur 6 axes, 3 linéaires et 3 rotatifs, permet par ailleurs une caractérisation optimale du produit.
L’essai combiné regroupe l’ensemble des contraintes appliquées précédemment.
La partie thermique du profil, vitesse de transition en température, durée et niveau d’exposition en températures basse et haute.
Le premier cycle en température est réalisé avec un niveau constant d’accélération de l’ordre de 3 à 5 Grms. A chaque cycle, cette valeur est augmentée du même incrément que dans l’essai précédent de tenue aux vibrations.
Le taux de mise en évidence de défaillance élevé (20%) pour un équipement ayant déjà bénéficié d’amélioration de robustesse pour chaque contrainte séparée met en évidence l’influence de la température dans les phénomènes de réponses aux contraintes mécaniques et justifie le bien-fondé de l’application des contraintes combinées en fin du procédé HALT.
Méthodologie des essais HASS
La méthodologie HASS met en œuvre des essais combinés vibrations, températures et VRT appliqués en cycles.
Avant de systématiser l'application du HASS en tant que procédé de contrôle de la chaîne de fabrication, le profil de test définissant les contraintes à appliquer doit être défini, le montage de la chambre destiné à accueillir tout ou partie de la production doit être optimisé et le Proof Of Screen (POS) doit être validé.
Le profil HASS est déduit des essais réalisés en HALT.
Le profil de test du HASS est déduit des contraintes ayant dû être appliquées pour caractériser le produit en HALT après que l'ensemble des actions correctives ait été pris en compte.
A titre d'exemple, le profil initial avant validation du POS peut se construire autour d'une excursion en température à 20% des limites opérationnelles détectées en HALT avec toutefois un delta minimal de 100°C et avec un niveau d'accélération en vibration se situant à moitié du niveau entraînant la destruction en HALT.
Le profil de HASS doit être validé par un POS qui prend en compte le montage de fixation des produits dans la chambre. Ce montage est un des éléments les plus délicats à réaliser dans le cadre du HASS puisqu'il doit permettre un passage simultané en test d'un maximum de produits en garantissant que chacun d'eux sera soumis aux mêmes contraintes mécaniques et thermiques.
Dès lors que la caractérisation en HALT fait apparaître des marges suffisantes entre les limites de fonctionnement et les limites de destruction, le profil du HASS se décompose en deux phases, l'une dite de précipitation qui, en faisant appel à des niveaux de stress supérieurs aux limites fonctionnelles, mais inférieures aux limites de destructions, transforme les défauts latents en défauts patents, et l'autre de détection avec des durées d'exposition aux températures haute et basse suffisantes pour dérouler les tests de bon fonctionnement et découvrir les défaillances.
Le POS s'effectue une fois les paramètres du HASS déterminés. Il consiste à appliquer au même nombre de produits que prévu par le montage 20 à 50 fois le cycle de test défini en HASS en combinant aux produits issus de la production série des produits tests incorporants des défauts de fabrication (tels des fils incorrectement soudés). L'objectif du POS est d'ajuster le profil du HASS pour que les défauts soient détectés si possible dès le premier cycle, mais sans induire de défaillances sur les produits "sains" ou réduire de manière significative leur durée de vie.
Ce dernier aspect est vérifié en comptabilisant le nombre de cycles nécessaire pour que les produits sains développent des défaillances symptomatiques d'une fin de vie.
Une fois le POS effectué, le HASS peut être appliqué en production.
Groupe Emitech - Mentions légales